在汽车发动机装配线上,左臂托举12公斤缸体,右臂同步完成6颗精密螺丝的±0.02mm定位拧紧——这组曾需要8名工人的工序,如今在富唯智能富智1号的双臂间一气呵成。其单臂8kg负载的设计,恰如精密制造领域的黄金法则:既满足工业场景中90%零部件的重量需求,又确保微米级操作的绝对稳定性。
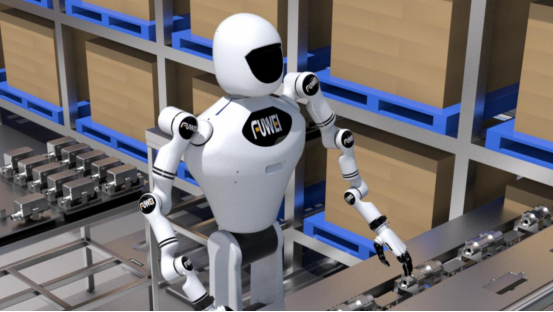
一、负载与精度的科学平衡
富智1号的8kg负载绝非偶然数值,而是深度匹配工业装配场景的精准定义:
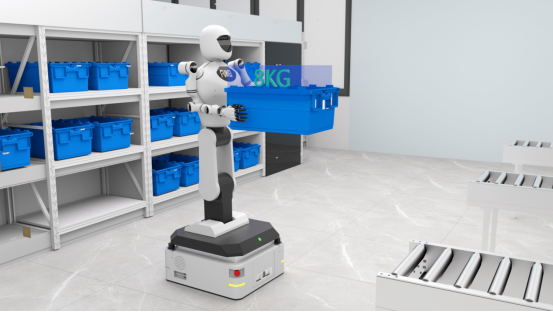
1.仿生力学架构:双臂采用七自由度关节设计,在三维空间灵活运动的同时,通过分布式驱动系统优化力矩分配,使8kg负载下仍保持±0.02mm-±0.05mm的重复定位精度;
2.动态抗扰能力:装配过程中突发外力扰动时,六维力传感器实时反馈数据,驱动关节电机在10ms内完成力矩补偿,确保重载下的操作稳定性;
3.轻量化博弈:相比巨蟹智能50kg重载机械臂聚焦搬运场景,富智1号以碳纤维复合结构实现自重与负载比1:0.4,避免因机械臂自重惯性影响精密装配质量;
二、负载能力如何转化为产业价值
在深圳某芯片工厂的实战中,8kg负载能力成为效率突破的关键支点:
双臂协同倍增效应:左臂移载晶圆盒(5.2kg)同时,右臂执行0.2mm间距芯片贴装,单机替代3台专用设备,效率提升至每小时450件。
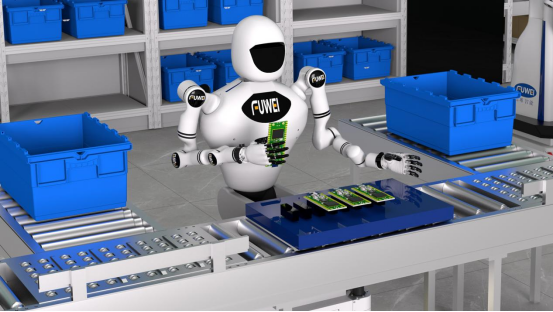
1.柔性生产核心支撑:白天装配7.8kg手机主板夹具,夜间切换搬运6kg电池模组,负载余量保障了跨场景切换安全性,设备利用率提升至92%。
2.汽车装配革命:某全球零部件厂利用8kg负载能力,实现发动机缸体(7.5kg)固定与螺丝同步拧紧,将8道工序压缩至单工位,良品率提升至99.97%。
三、负载背后的智能系统
富智1号的负载能力本质上是其“手眼脑脚”系统协同的产物:
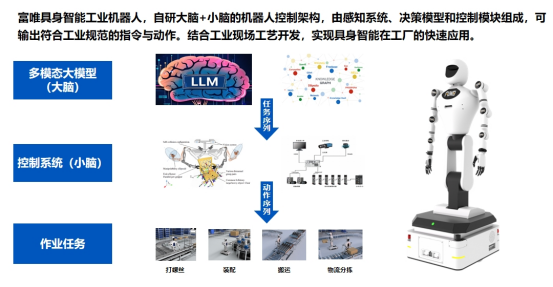
1.决策大脑预判力学环境:GRID任务规划大模型在操作前预演装配路径,结合语义地图提前规避大惯性动作,降低突发负载冲击风险。
2.视觉系统动态校准:双RGB-D435i相机在抓取8kg物体时实时监测形变,通过点云数据补偿±0.2mm位姿偏移,确保重物精准落位。
3.边缘控制器即时响应:一体化控制系统将力控指令传输延迟压缩至5ms,使负载状态变化瞬间触发关节力矩调整。