在精密制造领域,CNC加工的每一秒都关乎成本与质量。当传统人工上下料模式遭遇产能瓶颈、精度波动等难题时,自动化上下料已成为行业突破发展桎梏的关键选择。富唯智能轮式人形机器人的实践数据显示,采用自动化上下料的CNC车间,综合生产效能可提升300%以上,这背后是技术迭代对制造业的深度重塑。
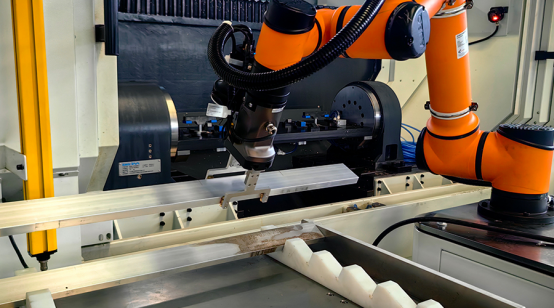
一、效率革命:打破人工操作的天然局限
人工上下料存在难以克服的效率天花板。一名熟练工人日均最多完成 800次CNC机床换料,且需在不同设备间往返奔波,实际有效作业时间不足 60%。而富唯智能轮式人形机器人搭载的 GRID 智能任务引擎,可实现12台机床的无缝衔接,单台设备日均上下料量达3600次,相当于4.5名工人的工作量。在3C电子精密加工车间的实测中,机器人能将设备待机时间从人工操作的15分钟 / 小时压缩至2分钟以内,使机床利用率从 65% 跃升至 92%。
自动化系统的连续作业能力更凸显优势。金属加工车间推行 “黑灯工厂” 模式后,富唯智能机器人在无人值守状态下可维持 720 小时不间断生产,期间完成 28800 次物料转运,而传统三班制人工团队在此期间至少需轮换9名工人,还可能因交接班衔接问题产生 3% 的物料误操作。
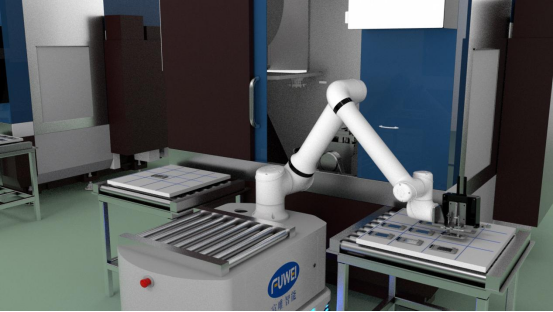
二、质量管控:从 “人控” 到 “数控” 的精度跃迁
CNC加工的核心竞争力在于微米级精度控制,而人工操作的不稳定性成为质量隐患。某汽车模具厂数据显示,人工上下料导致的工件装夹偏差占质量缺陷的 42%,平均每月产生 2.3 万元的废品损失。富唯智能轮式人形机器人 ±0.1mm 的末端重复定位精度,配合视觉定位系统,可将装夹误差控制在 5μm 以内,使产品合格率从 89% 提升至 99.7%。
自动化系统的过程追溯能力同样关键。机器人每次上下料都会自动记录物料编号、装夹参数、加工时间等数据,形成完整的质量档案。当检测到尺寸超差时,系统能在 0.3 秒内触发机床停机指令,避免批量报废。这种闭环控制机制,让某航空零部件企业的质量追溯效率提升了 8倍。
三、安全升级:构建无人化防护网
金属加工环境暗藏多重风险,工件搬运过程中可能发生的碰撞、高温工件造成的。
当 CNC 行业从 “规模扩张” 转向 “精益制造”,自动化上下料已不仅是技术选择,更是生存战略。富唯智能轮式人形机器人通过重构 “人 - 机 - 料” 协同模式,让每一台 CNC 机床都释放出最大效能,这正是制造业向智能化转型的核心要义。